Find more staff
Role:
Department staff:
Research staff:
Teaching staff:
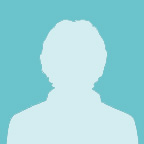
- Qualifications:BENG, MSc, PhD, FRAeS
- Position:Senior Lecturer in Aerospace Engineering
- Department:FET - Engineering, Design and Mathematics
- Telephone:+4411732 81100
- Email:Nihong2.Yang@uwe.ac.uk
About me
Dr Nihong Yang joined Uwe in January 2020. He obtained his PhD from The University of Birmingham in 1998, and then worked as a research fellow for The University of Southampton for about two years. In 2001, he joined Airbus UK to work in aircraft structural design and analysis, and since then had taken part in development of various aircraft programmes from the early A340 to the latest A350 and involved in many research projects. In 2010, he moved to China to work for Shanghai Aircraft Manufacturing Company as the Vice Director and a Senior Expert of the Composite Centre. He came back to UK in 2014 to work for QuEST Global Engineering as the Head of Fatigue and Damage Tolerance of the Aerostructure Centre. From 2018 to 2019 he worked as a consultant for Assystem.
Currently, Nihong's research focuses on structural design and optimisation, including topology optimisation of aircraft structures, composites, and applications of machine learning techniques in aircraft structural design and manufacturing. He is also teaching courses in the fields of structures and composite engineering. He is the programme leader of Aerospace Engineering.
Area of expertise
Dr Yang is experienced in aircraft structural design, analysis and test. He is familiar with aircraft structures, structure design requirements and process, structure analysis methods and test. He is an expert in aircraft composite structures and has personally designed, assessed and manufactured various monolithic and sandwich composite structures. The areas of his expertise include:
- Fatigue and damage tolerance of metallic and composite structures (fatigue spectrum, fatigue life, fatigue crack propagation, impact damage, and F&DT test)
- Composite structure design rules and considerations (layups, stacking sequences, fatigue sensitive features, environmental and aging effects, and composite design philosophy)
- Composite structure instability assessment (local and global buckling, initial and post buckling, super-stringer and multi-bay panel buckling, coupling effects of in-plane and out-of-plane loads, and instability test)
- Composite structure manufacturing (composite material qualification, pre-preg hand layup and ATL, RTM, and tooling)
- Optimisation of aircraft structural design and manufacturing (multi-level optimisation, topology optimisation, applications of machine learning techniques in design and manufacturing)
Publications
